
“Typically, wall sheathing is put only on the outside of the home but SIPs have it on both sides, inside and out, which adds significant strength and stability to the home,” Stephen says. SIPs create a wall system that’s two to three times stronger wall than standard stick frame construction. Of course, the size of your home and the thickness, material and type of insulation you choose for your roof also plays a factor in how energy-efficient your home will be. Even where wall thickness is the same, SIPs outperform stick framing on whole-wall energy performance by 40 to 60 percent. SIPs cut heating and cooling costs by as much as 60 percent over products used for conventional construction. “Energy codes are getting more and more stringent … but SIPs already meet those much stricter air-tightness requirements,” Stephen explains.Ī 2-by-6 stud-framed wall using R-20 fiberglass batt insulation achieves an effective R-value of 16.8, while a 6.5-inch-thick SIP wall can reach R-22 or higher. In addition to shaving time and labor expenses off your build, choosing SIPs can reduce your long-term energy costs, too.
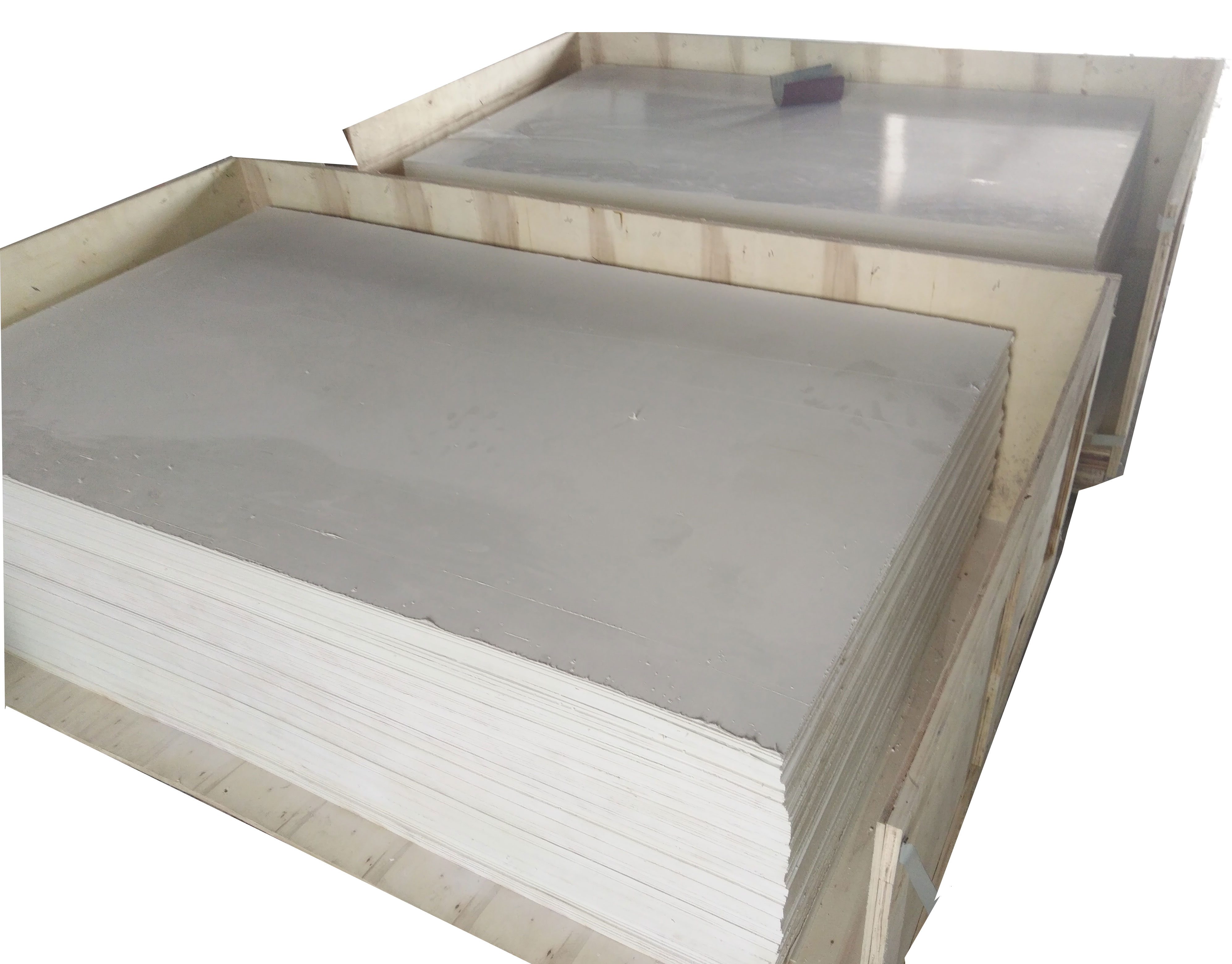
Often, a home can be enclosed within days or even hours.
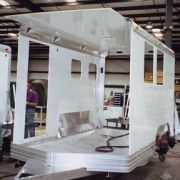
#Fiberglass sip panels install#
SIPs generally weigh less than four pounds per square foot, making them light enough to install by hand, though a crane may be used to hoist larger panels to the roof or for transporting bundles of SIPs to the site. Stephen explains that it’s not only the accuracy of the cutting, but the lightness of the panels that allows them to be transported around the building site and installed quickly. When they arrive at the job site, they’re easier to assemble.” This results in less wasted materials and onsite resources. That process mirrors the SIP process, where the SIPs are manufactured and cut to size and shape in the factory. “Timbers are fabricated and fit together in a factory, then they go out to the site and are put together. “I think the first benefit is the speed at which you can assemble them,” Stephen says.

Just take it from Stephen Munn, the general manager of SIPs manufacturer Insulspan. One thing that may strike consumers at the outset is the higher up-front cost of SIPs, but their abundant benefits more than make up for it over time (in dollars and comfort). SIPs have been a consistently reliable and strong choice since they arrived on the market, and the recent introduction of graphite into some versions has added an even bigger boost to their already impressive insulating properties. The white core is typically polystyrene, expanded polystyrene (most common), Styrofoam or polyurethane - the same durable-yet-lightweight foams used in bicycle and motorcycle helmets. Other materials used in SIPs include plywood or sheet metal, mainly in commercial applications.

The composition varies by manufacturer, but generally, a SIP is a solid core of insulation sandwiched between two layers of oriented strand board (OSB). The two mirror and reinforce each other’s strengths, from their sustainability to the swiftness with which they come together due to precision manufacturing. In construction, structural insulated panels (SIPs) and timber frame homes are a bit of a power couple.
